ã€Abstract】This paper introduces a mature induction heat treatment concept and method in Europe, which can directly improve the reliability and reproducibility of the induction heat treatment process. It is quick and easy to implement.
Induction heating and quenching equipment are available in most heat treatment workshops or sections. Induction hardening equipment in many companies is only a supplement to heat treatment. In general, unimportant parts or spare parts are inductively hardened, which is difficult to incorporate into important processes. This is mainly because the reliability of the induction hardening process or the stability of the product quality is difficult to guarantee for a long time, and it cannot provide stable load bearing capacity data, which greatly affects the selection and application of the induction hardening process by the designer. The reason is that the root knot is also the poor stability of the induction hardening process. Therefore, in the industry, the quality of induction hardening products depends on the status quo of "master". The experience of the “master†determines the quenching quality of the part, but the induction quenching result of the next part is difficult to ensure that it is exactly the same as the previous one even if the “master†operates it personally.
Developed countries such as Europe and the United States also experienced the same dilemma as us in the 1960s. However, with the technological development of precision machining processes, CNC machine tools and machining centers have been applied on a large scale in the field of machining, and the concept of precision machining It is introduced into the induction hardening process, so that the stability and reproducibility of the induction quenching process are ensured, so that the induction heat treatment process is changed from an auxiliary process to a main process, and the advantages of efficient and convenient induction heat treatment are exerted.
This article will introduce a mature induction heat treatment concept and method in Europe, which can directly improve the reliability and reproducibility of the induction heat treatment process, with quick results and easy operation.
Current status of induction heat treatment process
1. Sensor production and storage
The inductor is a heating tool for induction heat treatment. According to the principle of electromagnetic induction, the geometric characteristics of the inductor are directly related to the heating result under certain electrical parameters. Therefore, the design and manufacture of the inductor are very demanding. However, the actual condition of the sensor is mostly hand-made in the heat treatment workshop (see Figure 1), and the storage is also stacked in the cabinet (see Figure 2).
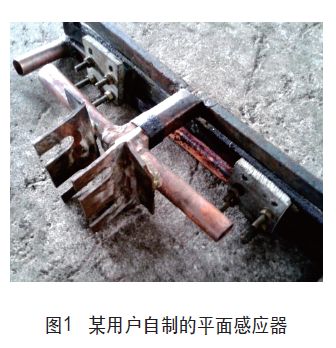
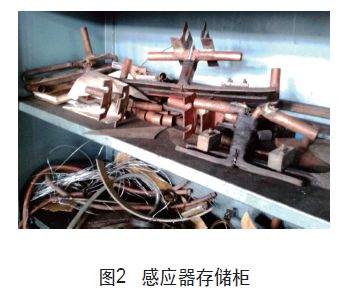
The shape of the hand-made sensor is irregular. In the future, the heat shape is inconsistent, and the temperature uniformity of the heating zone is poor. Even after repeated adjustments, the heating effect is barely acceptable. After use, it is removed and piled up together, which inevitably does not collide or even deform. Affect the effect of repetitive use. If you need to make spare parts for the sensor, it is almost impossible to achieve two pieces of consistency. The consistency of such a process is also impossible to talk about.
2. Sensor connection
The sensor is an induction heating element that is typically connected to the output of the quenching transformer. In order to adapt to the spatial position, there is often a transition guide between the inductor and the quenching transformer. At present, the connection between the quenching transformer and the inductor (or transition guide) of many equipments depends on several bolts, and the transition guides are rigid, as shown in Fig. 3 and Fig. 4.
This type of connected sensor does not guarantee the consistency of the two installation positions or the state of the sensor during quenching heating.
3. Cooling water and quenching liquid
The most common method of cooling water connection is shown in Figure 3. When the connection method is plugged, the sensor is deformed to affect the positional accuracy. More importantly, due to insufficient cooling of the guide plate, the heat is severe, and the sensor is displaced during the working process, resulting in a difference in heat treatment results.
The same is true for the connection of the quenching liquid. The unreliable quenching liquid connection and the quenching cooling mode cause the quenching cooling effect to fluctuate and cause cracking in severe cases.
4. Reliability and automation of the equipment
The reliability and automation of the equipment is also a factor influencing the reliability of the process implementation. It is difficult to meet the requirements for the quality stability of industrial products by relying on the experience and responsibility of “peopleâ€. And relying on the automation of machinery and equipment can achieve the same processing state. However, since the reliability and automation of equipment are generally related to investment, and the scope of investment is large, it is generally not determined by the application level of the workshop. Therefore, the main discussion is not made here.
Problems and gaps
The characteristics of induction heat treatment are the same as the machining mode, and they are processed one by one; while other processes using furnace heat treatment are characterized by multiple pieces of the same furnace. The quality control target for the same furnace processing is a furnace (batch), and the induction heat treatment can achieve quality control for each workpiece. Of course, if process repeatability is not reliably guaranteed, it will result in inconsistent results for each part of induction hardening.
The principle of induction heating tells us that the consistency of heating depends on the consistency of the sensing sensor and the consistency of the sensor-to-workpiece coupling. In addition to heating, another important factor in the operation of the heat treatment process is cooling, and the consistency of the cooling conditions (including temperature, pressure, flow, distribution, and angle) is equally important.
Comparing the current operational status and process principle requirements of induction heat treatment, we summarize the problems and gaps in the induction heat treatment operation as follows.
Sensor production
The sensor design and production are highly specialized and generally require special training. However, many heat treatment plants in China do not have special designers and capabilities to carry out complete sensor design, but based on the experience of the "master" on-site production. It can be seen from Fig. 1 and Fig. 2 that the inductor is made with a high degree of randomness, and there is basically no standardized sensor manufacturing method and method. The material is not standardized, the dimensional accuracy is low; there are many hand-welded surfaces and the shape is irregular. The electrode connection surface is not flat and the surface condition is poor.
The sensor is mainly composed of a sensor seat, a bus bar and a working coil (see Figure 5). The sensor base is the foundation of the inductor, and should have sufficient strength and strict dimensional accuracy, so as to give the working coil a reliable position basis; the bus bar is mainly for conveying current, and is also used for adjusting the coil and the sensor seat. The distance between them, therefore, the flow area and cooling is the core to be guaranteed; and the working coil is subjected to electromagnetic force when heated, so the strength of the busbar should also be considered. The importance of the working coil is self-evident, and it takes a lot of current to work, and its geometry determines the shape of the heating zone, which usually gets more attention. Cooling is an important factor affecting the life, so ensure adequate cooling.
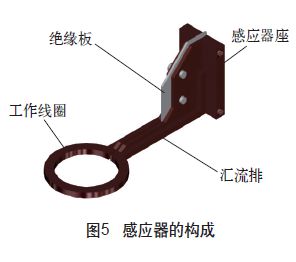
Another important issue in sensor manufacturing is the consistency of spare parts. Since the inductor has a certain service life, an alternative to a sensor that has been commissioned and produced for production must have the same dimensional accuracy, and it is obviously difficult to achieve it by hand.
2. Sensor connection
Since different parts require different sensors, it is necessary to frequently change the inductor and the quenching device to suit the production needs. The connection of the inductor must ensure the reproducibility of the mounting position, the reliability of the electrical contact surface, and the sufficiency of cooling.
As can be seen from Fig. 3 and Fig. 4, the conventional fork-type connecting guides cannot be positionally reproducible by bolting.
On the electrical contact surface of the inductor, due to the poor flatness of the surface, even if the bolt is pressed tightly, the effective contact area cannot be ensured, thus increasing the contact resistance, causing severe heat generation and formation of scale during use, and the scale is reversed. Increased contact resistance increases, resulting in greater power loss and heat generation.
The transition guide is a common device for connecting the quenching transformer and the inductor. The function is to adjust the position of the heating coil relative to the output of the quenching transformer, while providing an installation basis for the inductor. It can be seen from the foregoing that in order to ensure the position reproducibility of the inductor, one transition guide plate needs to have sufficient rigidity; and second, there must be positioning measures on the joint surface thereof, so as to ensure the position of the sensor for multiple disassembly and assembly; Since the transition guide is also a current-carrying conductor, there is significant heat generation during operation, and water cooling is generally employed. If the water cooling is insufficient or the water plates of the guide plates are not uniformly water-cooled, the deformation caused by the heat is different and the bending occurs. The position of the sensor can also change and the reference is lost.
3. Cooling state of cooling water and quenching liquid
Since cooling water and quenching fluid work on the inductor, both in terms of positional accuracy, longevity, and quenching results, monitoring and protection is required. At present, most old machine tools do not have the monitoring and alarm function of cooling water, or some use a simple pressure gauge to indicate. The gauge still indicates a high pressure condition when the line is blocked, but it does not indicate that the cooling water is sufficient. At present, the imported induction heating equipment uses flow monitoring and temperature monitoring for cooling, so that the state of cooling or quenching is fully ensured.
Solution - use sensor companion
The sensor partner draws on the advanced concepts of Europe and is the basic component for the user to solve the standardization and consistency of sensor production.
It fully considers the process characteristics of induction heat treatment, and has fully optimized the design from structural strength, water and electricity connection, condition monitoring and protection, so that induction heat treatment workers focus on the design and debugging of working coils, other consistency and reliability. The integrated water and electricity connection is guaranteed by the sensor partner. The sensor companion includes sensor boots, quick-change guides, sensor calibration dies, and sensors to make standard materials.
Sensor shoe
The sensor shoe (see Figure 6) is designed as a hydro-electric integrated quick connection mode. The plate is made of specially-rolled electric pure copper profile, CNC machining center, high dimensional accuracy, less welding surface and low inductance. The insulation and fastening between the plates are made of Teflon, which has good insulation performance and high heat resistance temperature. The length of the take-over can be shortened as needed; the mounting holes are reserved on the guide plate and can be used to fix other accessories.
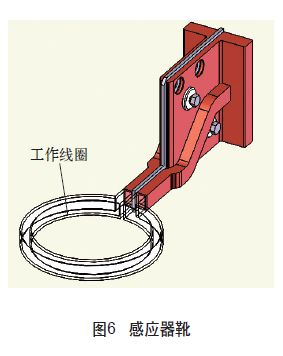
As can be seen from Fig. 6, as long as the user welds the working coil (inductor head), the heating can be debugged. Easy to use and interchangeable. Due to the high dimensional accuracy of the base of the sensor shoe, the mounting and positioning requirements of the sensor are also guaranteed. This allows the user to focus on the design and improvement of the heating coil section without having to spend time on the preparation of those basic components.
2. Quick change card holder
A connection guide is often connected to the output of the quenching transformer. The connecting guide in the sensor companion takes into account the quick connection function of the water and electricity, and more importantly, it provides the rigid and precise positioning of the sensor, ie the quick change deck (see Figure 7). The quick change card holder adopts a wedge-in structure, and the wedge-shaped bayonet is precisely matched with the base of the sensor shoe; the cooling water of the guide plate is sealed into the working coil of the inductor through the O-ring of the interface, and then returned to the guide plate; The brass clamps of the quick change deck need to be opened to replace the sensor and the water and electricity are completed at one time.
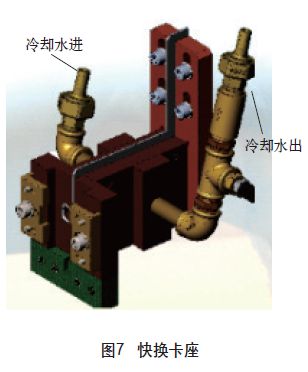
Since the connecting guide of the quick change card holder has good rigidity and cooling to the inner passage, the position accuracy of the sensor end during the working process is ensured, and the side cooling water is only once accessed, and is not disassembled with the sensor replacement. Temperature or flow monitoring can also be provided at the cooling water connection if required, which is more reliable.
3. Sensor correction protection mode
Once the sensor is put into use, it will be affected by the electromagnetic force during the working process, and a certain deformation will occur after a long time; even the external force may be deformed during the replacement of the storage and movement process. So, how do you guarantee that the sensor is intact the next time you use it? Drawing on the storage concept of the tool, we advocate the use of sensors to correct the protection mode. As shown in Figure 8, the protection mold has sufficient rigidity and positional accuracy. When the removed inductor is placed in the mold cavity, the deformation is corrected. If the mold cavity is stored or transferred together, the sensor will not be deformed or Damaged to ensure the integrity of the sensor when it is next in use.
4. Sensor manufacturing standard materials
Since induction heat treatment is a very professional field, there are few heat treatment technicians in the inductor, and there is insufficient understanding of the standardization of the inductor. Therefore, the specialization of the sensor manufacturing is very low. Most users can only use the common copper plates (tubes) on the market when they make their own sensors, and these materials often cannot meet the needs of sensor manufacturing. For example, a rectangular copper tube, the rounded corners are too large to affect the distribution of the heating layer. In addition, the different functions of the various parts of the inductor have different quality requirements for copper. Now, the series of profiles produced specifically for the manufacture of sensors can be selected from the sensor companion series. In addition, the insulating parts, fasteners, cleaning materials, etc. suitable for the sensor are currently selected in the sensor companion series, which greatly improves the geometric precision of the self-made sensor and improves the stability of the process execution.
5. User benefits
A new product to achieve reliable induction hardening requires very cumbersome steps and requires a lot of time and effort to design and manufacture the inductor and process.
First of all, the design of the quenching sensor (mainly the working coil) needs to be repeatedly modified in combination with the equipment capability and the designer's technical reserve, and then put into a complicated manufacturing process; after the manufacturing, the actual heating and debugging is required, and the chip verification is repeated to finally determine the sensor. The geometry and a complete process, and this process requires a series of assurance measures to achieve. Sensor companion is the guarantee for process reproducibility. Otherwise, whether it is sensor replacement or sensor re-production, all process development processes are lost, the same work must be done again, or with experience, back to the old road where only the master can do good products. . The use of sensor companion can ensure the process, no worries about quality fluctuations, even if the "master" is absent, can produce the same quality products, greatly improving production efficiency and reducing production costs.
Conclusion
For a long time, China's induction heat treatment industry generally relies on experience to ensure quality is far from meeting current requirements. An important reason for this is that no implementable measures for process reliability assurance have been found. The launch of the sensor companion has found a way for us to retain the wisdom of the “masterâ€, thus improving the reliability of the process and product quality, and achieving standardization and serialization of related tooling, greatly improving efficiency and reducing The cost.
Flexible Sprinkler Hose
Flexible Sprinkler Hose,Flexible Sprinkler Hose For Commercial Building,Flexible Sprinkler Hose For Industrial Duct,Sprinkler Flexible Hose Pipe
Hangzhou Ehase-Flex Co.,Ltd. , https://www.ehasetech.com