Chemical vapor deposited diamond retains the properties of natural diamond. Its high hardness and modulus of elasticity guarantee very high dimensional stability and wear resistance. Like natural diamond, chemical vapor deposited diamond has a low coefficient of friction, so the cutting force and power consumption are low, frictional heat is very low, and the formation of built-up edge can be prevented during cutting.
These anticorrosive coatings have a long service life when used for cutting corrosive polymers such as phenolic resins for composite materials, and they also prevent corrosive damage of the cutting fluid.
Diamond coated tools specialize in the processing of abrasive non-metallic materials, non-ferrous metals and abrasive non-ferrous metals. However, the chemical instability of diamond and metal alloys containing iron, nickel or cobalt limits the use of such coated tools in the cutting of non-ferrous alloys and superalloys.
Crystal Chemical Vapor Deposition Diamonds Many coatings are called diamonds, but chemical vapor deposition diamonds are the only coatings that use 100% true diamond crystals.
Diamond consists of pure carbon atoms and is arranged in a unique crystal orientation for unique physical properties. At 9,000 to 10,000 Vickers hardness, the hardness of the crystal diamond is almost twice that of the amorphous, diamond-like coating (DLC).
An amorphous diamond, or diamond-like coating, is a carbon film coated by a physical vapor deposition (PVD) process. These films are thinner than diamond films coated by chemical vapor deposition processes.
They have no crystal structure and typically have a lifetime of 10-15% of chemical vapor deposited diamond coated tools.
Unlike the application of metal-sintered polycrystalline diamond (PCD) on the tool to form a diamond tip, the chemical vapor deposited crystal diamond coating allows the entire tool surface (including tools with complex geometries) to be protected by superhard materials. The ability to coat such unique geometries makes chemical vapor deposited diamond coated tools a more significant advantage than polycrystalline diamond tools, and the latter is very costly to grind.
A physical vapor deposited coating with a metal-nitride, such as titanium aluminide (TiAlN), has a microhardness of only 1/3 of that of crystalline diamond.
The advantages of chemical vapor deposited diamond coated drills compared to tool tip polycrystalline diamond drills are fully demonstrated in carbon fiber drilling applications, reducing single hole costs by more than 70%. Chemical vapor deposited multi-layer diamond drills can process 300 through holes in composites before burrs and delamination, while PCD tip drills can only process 150 through holes.
Crystalline diamond is formed during hot wire chemical vapor deposition, and the process takes 20-40 hours. The temperature used in this process is 1,500 °F (815.5 °C) to prevent the application of anything other than solid carbide. The precise pretreatment process requires a 6% grade of cemented carbide for optimum adhesion.
Without pretreatment, there is almost no chemical bond between the diamond and the carburized cemented carbide. However, the diamond can be embedded in the rough cemented carbide surface and adhered to the surface by mechanical interlocking of the cemented carbide and diamond.
A tool containing 10% cobalt can be coated, but additional processing is required to achieve good adhesion and the coating process is expensive. The coating technology itself has also made significant progress as companies strive to increase deposition rates and develop new pretreatment methods.
Roger Bollier, president of Multilayer Diamond Diamond Tool Coating LLC (), said: "At first, only a single layer of polycrystalline diamond could be formed on the tool."
Bollier said: "But recent technological advances have made it possible to form nanoscale crystal diamonds. Nanoscale crystal structures can produce very smooth surfaces and maintain sharp edges, which can greatly reduce delamination in the processing of carbon fiber composites."
He added: "The combination of polycrystalline and nanocrystalline crystal diamonds into interlocking layers can form the best diamond coating, and multilayer diamond coatings have become an option for all non-ferrous metal coatings."
The multilayer of nanocrystalline diamond increases the fracture toughness of the coating. In addition, the micro-grain structure of submicron crystals can form a smooth surface on the cutting edge for fine surface finish, which can reduce the formation of built-up edge when processing viscous non-ferrous metals. These coatings also extend tool life in dry or minimally lubricated aluminum alloys.
A common failure of all coatings is cracking. That high and independent polycrystalline diamond structure tends to create cracks along the line of weakness that directly enters the substrate. Once the coating has this problem, the entire coating will peel off.
However, the nanocrystalline diamond produces cracks at a 45 degree angle to the substrate. The staggered polycrystalline and nanodiamond crystal layers constantly change the direction of the crack formed during processing, thereby increasing the lifetime of the diamond coating by 40%.
.jpg)
In general, graphite diamond coated tools are 10-20 times longer than uncoated tungsten carbide tools. Therefore, with them, unattended machining can be performed, and multiple workpieces can be completely machined with one tool. Significantly reduces wear and recalibration of the tool.
In composite applications, it is not uncommon to have a longer life. For high-density fiberglass, carbon fiber and G10-FR4, it has been reported that the lifetime of diamond-coated tools is 70 times longer than that of uncoated tungsten carbide tools.
Since it takes a long time to coat the tool with diamond, the pretreatment process required to achieve a diamond coated tool with good adhesion is costly.
Although diamond-coated tools cost about five times as much as high-quality carbide tools, they significantly reduce overall production costs because of their wide operating range and long life. For example, when an automobile manufacturer processes high-density fiberglass, it can increase the productivity by processing an end mill with 15 parts worth $15 instead of a diamond-coated end mill that can process 750 parts and cost $150. . This approach saves the company more than $600,000 a year.
As aerospace manufacturers increasingly use composite materials, engineers have realized that the proper combination of diamond coatings and tool geometries for specific applications provides the most efficient machining solution.
Composite materials such as high density fiberglass, carbon fiber and G10-FR4 are easily worn. If the tool is not properly pretreated, the wear of these materials may reduce the adhesion of the diamond film to the cemented carbide.
In an aerospace application, the Defense Manufacturing and Processing Center (NCDMM) and Diamond Tool Coating LLC are the drive shafts for processing Sikorsky Black Hawk helicopters (with an internal titanium liner, an IM7 carbon fiber tube and An external titanium end fitting) provides a "single knife" solution. This diamond-coated tool can produce high-quality holes with a processing cost of only a fraction of that of PCD tools.
In another application, NCDMM and Diamond Tool Coatings developed a diamond tool for machining high precision sighting systems from Lockheed Martin and Fire Control. Lockheed had previously had difficulty achieving high precision due to the very abrasive tool wear in abrasive applications. In applications where other coatings are spalled, chemical vapor deposited diamond coatings greatly improve tool life and part quality. .
How to Form a Diamond Coating The diamond coating is formed using hydrogen and methane in a vacuum chamber. Usually, these gases are added to the vacuum chamber in a ratio of 50:1, mainly hydrogen. High temperature elements in the vacuum chamber can cause deposition processes to occur. For example, sp3 Inc. () uses filaments heated to about 2,200 °C to dissociate methane into carbon and hydrogen. Then, the carbon atoms form crystal nuclei and grow into fine diamond crystals, and these fine crystals form a continuous diamond film over time. The diamond grows slowly, about 0.5 to 1.0 microns per hour.
It takes almost two days to incubate a 40 micron film on a blade, and most round knives require one night to coat.
Compared with the obsolete HPS,MH,HID,LED Vegetation Lights specific wavelengths that plants need in their photosynthesis,as led cost 50% less electricity but output higher PAR which receive warmly welcome from growers and gardeners,furthermore,as led Grow Light dissipate less heat during the illumination process,thus growers and gardeners don't have to install other cooling facilities to solve the overheating problems,which in turn save you much budget on plants growing project.
Philizon have over 6 years' experience in designing and manufacturing LED Vegetation Lights. Persuiting to offer the best grow lights for plants growth,we cooperate with the scientific research institutes and the Academies of Agricultural Sciences in USA, Australia Canada, UK and so on.A great number of commercial plant growers test the lights, and their feedbacks show that this lamp owns a lot of 640nm,660nm and 740nm lights, which gives the plants enough nutrient in the flowering and fruiting phase and bring a far higher yield than other LED Vegetation Lights in the market.
Full Spectrum LED Vegetation Lights and High PAR are good for growth Plants
Item Display
Advantages
Plug with listed certificate safe to use.
Ageing Test
Application
Ideal for all phases of plant growth, and works well with water solution culture and soil culture. Can be used in house garden, pot culture, sowing, breeding farm, flower exhibition, bonsai garden, green house, sowing farm, greenhouse cultivation, water soluble breeding, pipeline cultivation and so on.
Our Quality Control systems and after-sales
Package
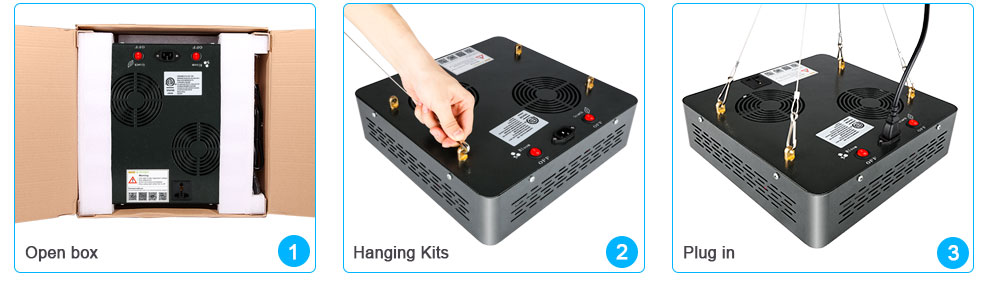
Warnings:
1.lndoor use only.
2.To avoid being damaged,do not use water or drip irrigation while using.
3.Sunshine lighting time should be 12-18 hours.
4.While irradiating the plants,the height of led grow lamp is not less than 10 inches,
low height will cause the destruction of plants.
5.Highly hang the lamp will weaken the energy and affect the growth cycle of the
plants, so the lamp should not be hung too high.
6.While taking care of the plants, please spray the leaves and branches 2-3 times everyday,
to ensure the the plants do not wrinkle a wither, and have no phenomenon of few fruit, and
hard pericarp.
Our Advantages
Professional: we are professional LED Vegetation Lights and LED Aquarium Light manufactuer here in China, you will get Professional and High quality LED Vegetation Lights and LED aquarium lighting from us and get good guarantee.
Cost-effective Price: we don`t have the lowest price, but the LED Vegetation Lights and Aquarium Light you get from us really cost-effective, good quality & decent price.
Win-win situation: Long term business is our mission, we think you will agree with us if you are running a business, so we will provide good led aquarium grow lights and warming service to build a long-term business relationship with you
24/7 unlimted customer service: we are always here for you for your question, any question just email us or call us, we will do our best to help you all the way.
Long term warranty: Don`t worry about the quality and we guarantee you 3years warranty for all the LED Vegetation Lights and coral reef led aquarium light..
Best buying experience: you will get the tiptop serive you have ever had,just have a try and you`ll see.
Trade Terms
Payment: T/T, L/C, Paypal, 30% deposits before production, 70% balance to be paid before deliverying(Western Union are welcome)
Sample will be delivered within 7 working days.
Discounts are offered based on order quanlityes.
MOQ:sample order are acceptable
Delivery ways:DHL,UPS,FedEx,TNT, door to door,by sea,by air,etc.
Warmly welcome to take a visit on our factory at any time and we can pick you up as you request.
High PAR Output Grow Light,Hydroponics Led Grow Light,Led Grow Light For Plants,Led Grow Light For Greenhouse
Shenzhen Phlizon Technology Co.,Ltd. , https://www.szledaquariumlighting.com