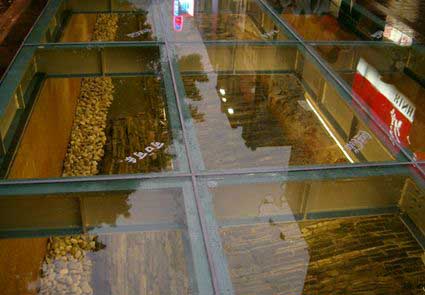
The glass floor is not just a product of screaming. The glass floor gives people a pure feeling of sky, letting people feel the natural light to travel in every corner. At the same time, the glass floor can make the space look more swellable and give an independent sense of space.
Architect Charles Barclay, who has already decorated many glass floor projects, said that people can no longer tolerate dark corridors and basements. Interestingly, he can help inject water under the floor. Even with the usual method, an unexpected floor is a glass floor.
The glass floor must have sufficient thickness to withstand the items on it, and it must be fire-resistant in some cases (mainly fire escapes, exits, aisles, and vestibules here). Therefore, glass floors are often made from two or three layers of glass, sandwiched or layered. The uppermost floor is a toughened structural floor that can support gravity.
Sandwiched together, sometimes because of the need for a fire-resistant gel layer, the glass plate will be seamlessly connected. According to different needs and design, the overall thickness of the glass floor is not the same, probably between 24mm and 46mm. Technical specifications usually need to be calculated and analyzed by structural engineers, according to the provisions of the working local government construction management regulations.
The size of individual glass laminates is also a matter of processing considerations, so that two or three glass layers up to a single glass floor can make 10,000 square meters. These are set in the frame, sometimes with hardwood, but more commonly steel.
If you work with an architect, they usually specify a glass manufacturer or buy a glass that is suitable for use as a floor glass and contact the Glass Association to purchase it. Pilkington is a good source of technical specifications and advice.
The glass floor surface can be kept clear, or etched and sandblasted (acid etching allows more precise control and less sandblasting than dense or heavy surface textures). Mostly due to the green color, several glass floors will give it refracted light (crystallized glass can avoid this, but generally should not be too strong). Blanket blasting, or grid pattern spots or streaks, are often used to provide non-slip glass flooring. Whether the surface of the transparent glass is anti-slip, it can be applied to highly polished marble floors.
Due to its wide range of uses, there are also many varieties of hook and loop sanding disc. The most commonly used are red sanding disc, yellow/gold sanding disc, green sanding disc, and white sanding disc, etc.
The sandpaper disc is using aluminum oxid abrasives, with grits as below: 40#, 60#, 80#, 120#, 180#, 240#, 320#, 400#, 600#, 800#, 1000#, 1200#, 1500#, 2000#.
The abrasive polishing disc can be punched into various shapes, round, round with holes, triangle, rectangle, iron shape, neckline shape, etc.
This product is round abrasive disc size: 100mm, 125mm, 150mm, 180mm, 225mm or other size can be customized.
The holes best selling is with 6 hole, 8 holes, 15 holes, 17 holes or customized.
The main purpose of our abrasive sanding disc:
1. Polishing of primer and finishing of paint, such as mid-coat paint/primer grinding of ships.
2. Polishing of synthetic materials, such as burr sharp edges and surface adjustment after plastic products are formed.
3. Grinding of metal and aluminum alloy to remove foreign matter and surface particles.
4. Suitable for making various specifications of brushed and self-adhesive sand discs.
This abrasive sanding disc is one of our main abrasive products, as the manufacture of abrasive tools, we mainly produce the Flap Disc Backing Pad, Flap Disc Adhesive, Abrasive Flap Disc, bonded abrasives( Cutting Wheels and Grinding Wheels ), Abrasive Machine , etc. So welcome more orders, we can offer you best quality product with best competitive price, please contact Emma.
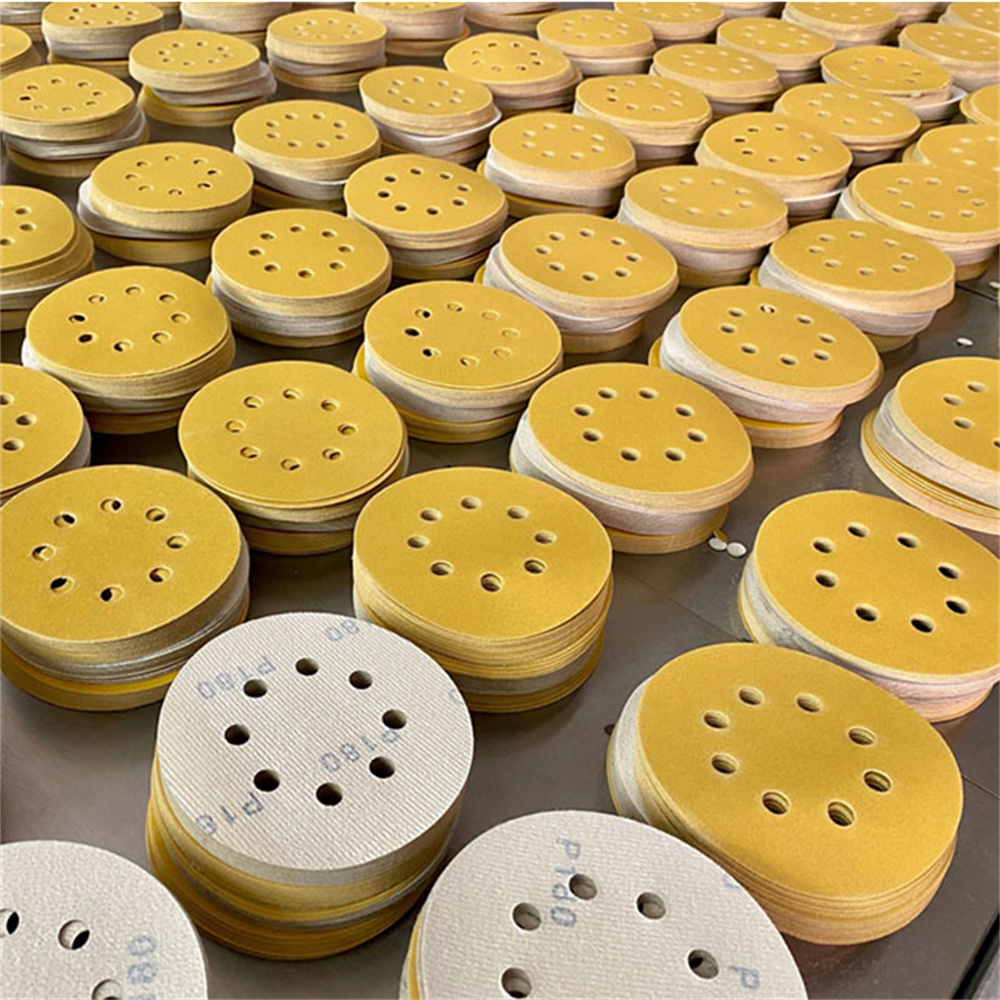
Abrasive Sanding Disc,Sanding Disc,Metal Sanding Disc,Abrasive Tools Sanding Disc
Zhengzhou Jiading Abrasive Manufacturing Co.,Ltd , https://www.jiadingabrasive.com