Home>Bearing knowledge>Analysis: Reasons for the overhaul of head bearings of air compressors |
Analysis: Reasons and conclusions of the overhaul of the air bearing head of the air compressor
/*250*250 was created on 2017/12/25*/ var cpro_id = 'u3171089'; |
As the unit is working, it is close to the main engine overhaul period; the life of the main bearing is gradually increasing to the maximum allowable time limit. At this moment, the axial and radial turbulence of the screw gradually tends to the maximum drawing response value; this change will cause the screw and the screw, The gap between the screw and the main body casing and the front and rear end faces is greatly changed. At this moment, the host operation is still safe; but it is now necessary to think about the time when the program organization overhauls the mainframe. After the overhaul period; the bearing wear and the host cooperation gap will reach the limit value of the host skill condition; at this moment, the host is in an unsafe operation; at any time, there are serious consequences:
1. The main machine load increases; the main motor and the electrical system form a hazard. The intense friction between the screw of the main machine, between the screw and the front and rear end faces, between the screw and the main body casing will cause the host work load to be sharply added; The working load of the severely worn bearing is also very large. As a result, the motor will be in an overloaded operation; it will seriously endanger the safe operation of the motor. If the situation is severe; if the air compressor unit is covered by the electrical equipment Insensitive or ineffective; it can also incur motor burning.
2. The air compressor exhaust volume will have a large fluctuation of attenuation.
The increase of the host cooperation gap will lead to a serious decline in the host power; that is, the air compressor exhaust volume has a large fluctuation of the fluctuation; it has a certain impact on the normal production of the gas unit. Especially for those air compressors, the amount of equipment is high. Smaller users; due to the air compressor exhaustion attenuation; in the case of relatively stable gas consumption in the gas system; the compressed air pressure of the pipe network will drop a lot; it will be able to present the gas system equipment, etc. Homework; then presenting an impact on the normal production of the unit or incurring a temporary shutdown; bringing losses to the company.
3, the most serious result is to present the host's "locked to death".
Once such a situation is presented; if the electrical protection system response is not timely or guaranteed to fail; the same can bring serious damage to the main motor and electrical system.
Regarding the disposal of the host "locked to death"; on the one hand, the repair cost of the overhaul will be much more expensive than the normal overhaul; on the other hand, the host component will be damaged; therefore, the modified function of the host will be worse than that of the normal overhauled host. If the severity of the damage to the host has reached the point of no correction or the original can not be corrected; it can only be used to replace the replacement of the new host; direct loss is the biggest. Because the cost of the new host is usually the purchase of the entire air pressure About one-third of the crew's cost; far higher than the normal overhaul cost of the mainframe; under normal circumstances, the inductive skill function and the new host of the overhauled host are very close!
In summary, the normal overhaul operation is not only the basic requirement for equipment protection; it is also the basic requirement for the company to control the normal equipment protection cost, prevent unnecessary capital loss and ensure the normal production of the company!
Therefore, it is not only necessary to carry out overhaul on the air compressor mainframe on time and according to the specifications; it is also necessary!
The screw air compressor mainframe needs to be overhauled:
Precisely; the time when the main engine is overhauled should be based on the expiration of the life of the bearing; however, it is actually difficult to have an accurate target to determine whether the service life of the bearing will expire or has expired; According to the practice of the world-renowned air compressor manufacturer based on its nearly 100 years of practice, the mainframe is overhauled after 20,000 hours or 4 years of compressor operation.
In addition to the above general specifications; based on the experience can also be more accurate from the following aspects of the host situation:
1) The sound when the main machine is working; especially if the bearing has abnormal noise,
2) motor operating current; especially the difference between the no-load operating current and the specification value,
3) Oscillation of the bearings of the head.
Our company has done the screw air compressor head overhaul brand: GHH; Rod CommScope; Ingersoll Rand; Atlas; Fusheng; Sullair; Liuzhou Fidelity; Bolete; TMC; Kobelco.
Recommend to friends comments close window
Bearing related knowledge |
The axial positioning and fixing of rolling bearings at the time of the store's bearing varieties are detailed and out of the misunderstanding of detecting bearing quality INA bearing - Insertion Roller Bearing device method - Determination of bearing clearance |
This article links to http://
Please indicate the bearing network http://
Previous:How to deal with the problem of overheating of imported bearings Next:The primary effect of internal combustion engine oil
Rolling Mill Bearing for blanking machine .
Rolling mill bearings are the bearings used on the roll necks and rollers of metallurgical, mining and other rolling mill stands. Cylindrical roller bearings are often used to withstand radial loads, deep groove ball bearings or angular contact ball bearings, or radial design or thrust design Tapered Roller Bearings to withstand axial loads. Most of them are lubricated and cooled by means of oil-air lubrication or oil mist lubrication.
Rolling Mill Main Application:
Cold rolling mill, Hot rolling mill, Blanking machine
Roll neck and drum for metallurgy, mining and other rolling mill stands
Model No.
|
ID (mm)
|
OD (mm)
|
W (mm)
|
Weight (kg)
|
FC2028104
|
100
|
140
|
104
|
5.2
|
FC202870
|
100
|
140
|
70
|
3.7
|
381040X2
|
200
|
310
|
200
|
55.6
|
380641
|
205
|
320
|
205
|
55.4
|
382040
|
200
|
310
|
275
|
75.1
|
FC2030106
|
100
|
150
|
106
|
6.8
|
FC202970
|
100
|
145
|
70
|
4.1
|
FC202880
|
100
|
140
|
80
|
4
|
FC202870M
|
100
|
140
|
70
|
3.7
|
FC202870/P6
|
100
|
140
|
70
|
3.7
|
FC2028104M
|
100
|
140
|
104
|
0
|
FC2028104/P6
|
100
|
140
|
104
|
5.2
|
FC2028104/P5
|
100
|
140
|
104
|
5.2
|
FC182870
|
90
|
140
|
70
|
4.4
|
381050X2/YA
|
250
|
460
|
270
|
192
|
382052X2
|
260
|
400
|
255
|
117
|
20FC1570
|
100
|
145
|
70
|
3.8
|
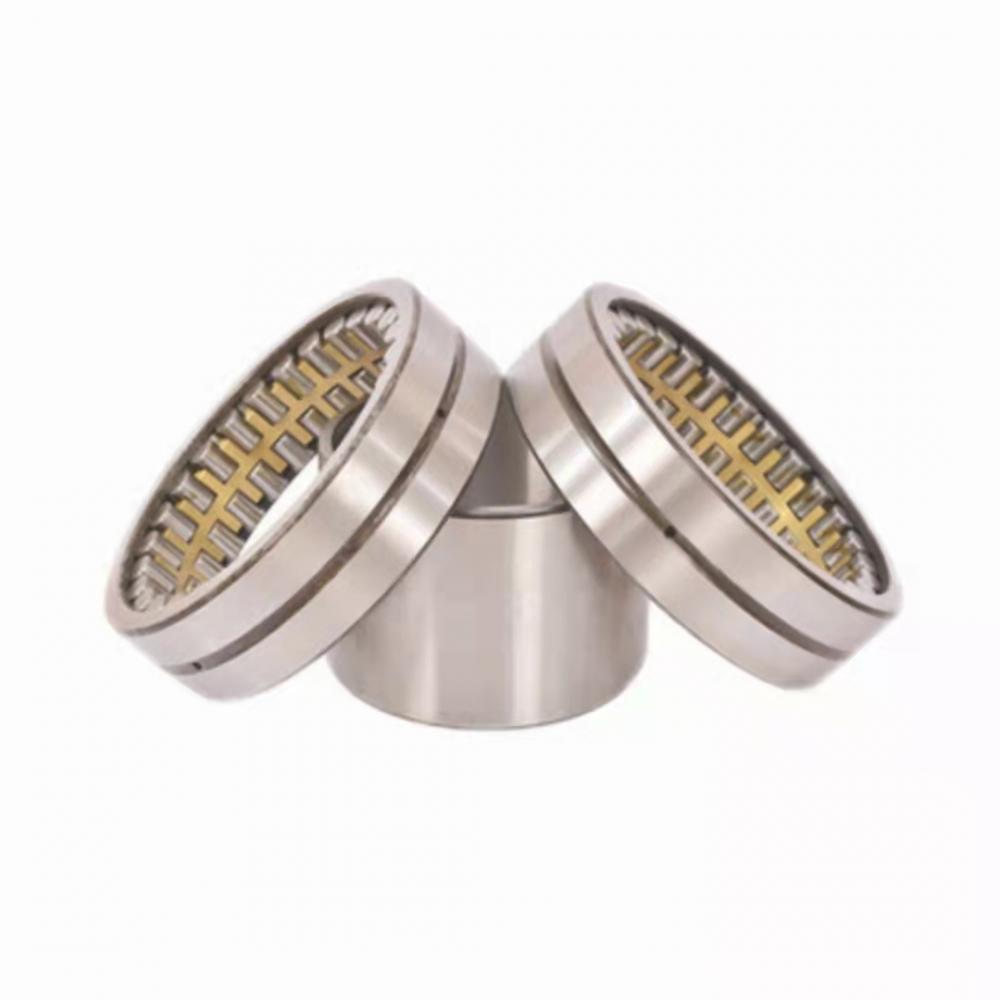
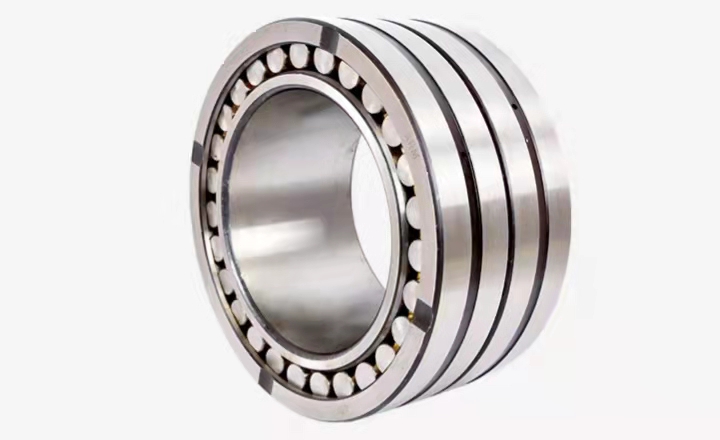
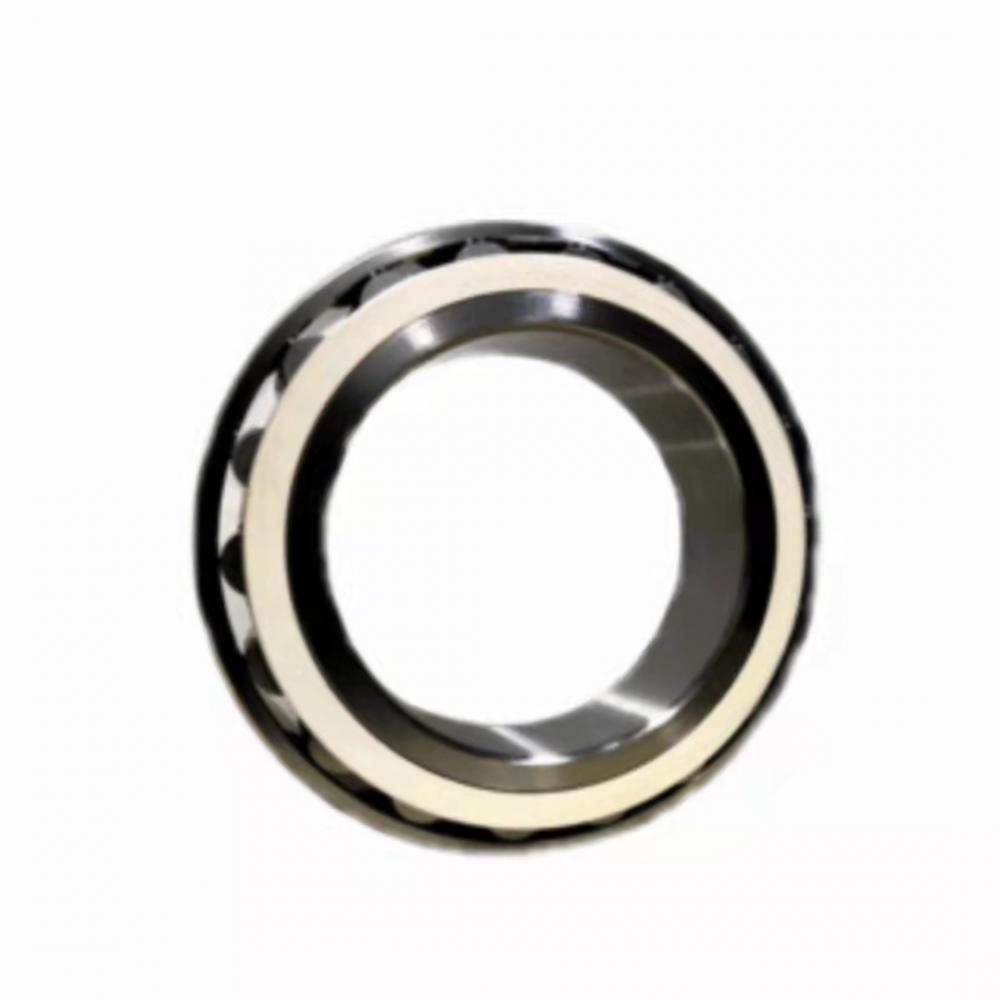
Fcd Rolling Mill Bearing,Fcd Rolling Bearing,Bearing For Steel,Bearing For Steel Mill
Shijiazhuang Longshu Mechanical & Electrical Equipment Trading Co., Ltd. , https://www.longsbearings.com